|
1、能耗分析 我們知道加、卸載控制方式使得壓縮氣體的壓力在Pmin~Pmax之間來回變化。Pmin是低工作壓力值,即能夠保證用戶正常工作的低壓力。一般情況下,Pmax、Pmin之間關系可以用下式來表示: Pmax=(1+δ)Pmin δ是一個百分數,其數值大致在10%~25%之間。 而若采用變頻調速技術可連續調節供氣量的話,則可將管網壓力始終維持在能滿足低工作壓力上,即Pmin附近。 由此可知,在加、卸載供氣控制方式下的空壓機較之變頻系統控制下的空壓機,所浪費的能量主要在2個部分: a、 壓縮空氣壓力超過Pmin所消耗的能量 b、 在壓力達到Pmin后,原控制方式決定其壓力會繼續上升(直到Pmax)。這一過程中必將會向外界釋放更多的熱量,從而導致能量損失。另一方面,高于Pmin的氣體在進入氣動元件前,其壓力需要經過減壓閥減壓至接近Pmin。這一過程同樣是一個耗能過程。 2、卸載時調節方法不合理所消耗的能量 通常情況下,當壓力達到Pmax時,空壓機通過如下方法來降壓卸載:關閉進氣閥使電機處于空轉狀態,同時將分離罐中多余的壓縮空氣通過放空閥放空。這種調節方法要造成很大的能量浪費。 關閉進氣閥使電機空轉雖然可以使空壓機不需要再壓縮氣體作功,但空壓機在空轉中還是要帶動螺桿或者活塞做回轉運動,據我們測算,空壓機卸載時的能耗約占空壓機滿載運行時的10%~15%(這還是在卸載時間所占比例不大的情況下)。換言之,該空壓機10%的時間處于空載狀態,在作無用功。很明顯在加卸載供氣控制方式下,空壓機電機存在很大的節能空間。 3、其它不足之處 (1)靠機械方式調節進氣閥,使供氣量無法連續調節,當用氣量不斷變化時,供氣壓力不可避免地產生較大幅度的波動。用氣精度達不到工藝要求。再加上頻繁調節進氣閥,會加速進氣閥的磨損,增加維修量和維修成本。 (2)頻繁采用打開和關閉放氣閥,放氣閥的耐用性得不到保障。一般的工礦企業空壓機一直都是全速運行,正常情況空壓機設計時將這部分多余的能量通過溢壓閥放掉了,溢壓閥放的能量越多,那么浪費的電能就越多;新型的空壓機雖已采用自動控制,當氣壓到達設定值時通過調節進氣量來調整做功量,當到達設定值時關閉進氣閥讓電機空轉,這樣雖可節約一部分電能,但據我們實測,空轉時的電流只是降?醬蜓故鋇囊話氳緦鰨ㄈ繅惶?5KW空壓機,打壓時電流為100A到120A,空轉時電流也有60A左右),都存在電能的巨大浪費。 四、改造方案 空氣壓縮機恒壓供氣智能控制系統是由變頻器、壓力傳感器、智能控制器控制單元、軟件控制單元等組成。此控制系統根據壓力傳感器檢測到的空壓機出口的壓力值,通過智能控制器進行計算,然后輸出信號調整變頻器輸出頻率,進而控制壓縮機轉速,在精確地控制空壓機出口的壓力的同時,延長壓縮機系統的使用壽命,并大幅度地節約電能。 我們可以把管網壓力作為控制對象,壓力變送器YB將儲氣罐的壓力P轉變為電信號送給PID智能儀表,與壓力設定值P0作比較,并根據差值的大小按既定的PID控制模式進行運算,產生控制信號送變頻調速器VVVF,通過變頻器控制電機的工作頻率與轉速,從而使實際壓力P始終接近設定壓力P0。同時,該方案可增加工頻與變頻切換功能,并保留原有的控制和保護系統,另外,采用該方案后,空壓機電機從靜止到旋轉工作可由變頻器來啟動,實現了軟啟動,避免了啟動沖擊電流和啟動給空壓機帶來的機械沖擊。
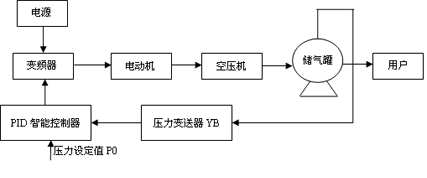
圖5 控制系統流程圖 由于用氣量的不斷變化,氣罐里的壓力也會變化頻繁。采用變頻調速系統用調整電機轉速的方法來調整壓縮機的供氣量。使氣罐內的氣壓始終保持在理想的狀態下,由于空壓機基本上屬于恒轉矩負載,用變頻調速的方法調整供氣量能使電機的輸出功率基本與轉速(供氣量)成正比關系,達到很好的節電效果。由于空壓機在啟動時,內部有少量的滯留氣壓,啟動和加減速運行時要求變頻器反應快速,因此,調節方式采用閉環自動調節,控制系統根據壓力傳感器檢測到空壓機出口的壓力信號值,經過A/D模擬數字轉換單元的信號轉換后,通過智能控制器和變頻器調整壓縮機電機的轉速,保證電機以功率輸出。 空壓機節電控制系統與空壓機原控制系統互為備用,兩套系統之間存在互鎖關系,以確保空壓機正常、安全運行。 五、節電原理 我們知道,用調整電機轉速的方法同樣可以調整供氣量。由于空壓機基本上屬于恒轉矩負載,用變頻調速的方法調整供氣量能使電機的輸出功率基本與轉速(供氣量)成正比關系,達到很好的節電效果。 如圖2 我們采用具有矢量控制功能的富士變頻器(或由用戶指定品牌的變頻器),?墑溝緇詰退偈幣材芴峁┞愀涸匭枰淖亍M保皇勘淦燈韉淖遠詰縋J劍墑溝緇諑愀涸刈匾笙亂宰钚〉緦髟誦校锏礁玫慕詰縲Ч?nbsp;
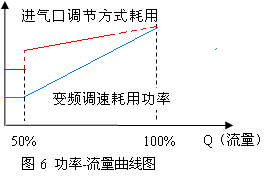
總之,采用空壓機節電控制系統后,不但可節約15~35%的電力費用,延長壓縮機的使用壽命,并可實現"恒壓供氣"的目的,提高生產效率和產品質量。 六、改造后性能 1、節約能源: 變頻器控制壓縮機與傳統控制的壓縮機比較,能源節約是最有實際意義的,根據壓縮空氣需求量來供給的壓縮機工作是經濟的運行狀態,節省電費約15~35%之間。 2、運行成本降低: 傳統壓縮機的運行成本由三項組成:初始采購成本、維護成本和能源成本。其中能源成本大約占壓縮機運行成本的77%。通過能源成本降低25%,再加上變頻起動后對設備的沖擊減少,維護和維修量也跟隨降低,所以運行成本將大大降低。 3、提高壓力控制精度: 變頻控制系統具有精確的壓力控制能力。使壓縮機的空氣壓力輸出與用戶空氣系統所需的氣量相匹配。變頻控制壓縮機的輸出氣量隨著電機轉速的改變而改變。由于變頻控制電機速度的精度提高,所以它可以使管網的系統壓力變化保持在3pisg變化范圍也就是0.2bar范圍內,有效地提高了工況的質量。 4、延長壓縮機的使用壽命: 變頻器從0Hz起動壓縮機,它的起動加速時間可以調整,從而減少起動時對壓縮機的電器部件和機械部件所造成的沖擊,增強系統的可靠性,使壓縮機的使用壽命延長。此外,變頻控制能夠減少機組起動時電流波動,這一波動電流會影響電網和其它設備的用電,變頻器能夠有效的將起動電流的峰值減少到低程度。 5、降低了空壓機的噪音: 根據壓縮機的工況要求,變頻調速改造后,電機運轉速度明顯減慢,因此有效地降了空壓機運行時的噪音。現場測定表明,噪音與原系統比較下降約3至7分貝。 6、系統穩定性能更強: 保存原軟啟動系統,本控制系統的變頻-工頻切換功能可以使變頻控制系統發生故障時將壓縮機電機切換到原軟啟動系統工頻工作,以確保壓縮機組可以正常工作。
|